媒体资源
现在位置:首页 > 活动&新闻 > 媒体资源
- 涡流探伤的原理是什么 能检测出哪些缺陷
- 时间:2018-04-08 发布者:本站 浏览次数: 分享至
在一些工程图纸的脚注上有时会出现这样一句话:“必须采用涡流探伤技术进行探伤”;但是却并没有明确指示应该对该组件上的哪个区域进行探伤,并且也没有指出利用涡流探伤的目的是什么:查找缺陷?验证热处理过程?还是螺纹探伤?工程师们都想利用一种成熟的技术来验证工程组件的质量问题,但是涡流探伤技术却不能作为一个全面的测试技术使用,因此,为了获得正确的探伤结果,充分理解这种探伤技术的原理、应用范围和操作方法是十分重要的。
涡流探伤技术主要是采用电磁场探伤金属制品表面和次表面上的缺陷。电磁感应科学是在19世纪中期发展而来,在19世纪后期,人们发现将线圈与具有不同电导率的金属接触时得到的实验数据会发生改变。在19世纪50年代到60年代,涡流技术逐渐发展成了一种广泛应用于核能和航空工业领域的新兴技术。
在涡流探伤技术中,将通电线圈放置在待探伤金属样品附近,金属样品内会感应出涡流。与不含缺陷的同种金属制品对比而言,制品中若存在缺陷或者结构发生改变都会导致涡流变化。因为涡流的分布和大小,除与线圈的形状和尺寸、电流的大小和频率等有关外,还取决于试件的电导率、磁导率、形状和尺寸、与线圈的距离以及表面有无裂纹缺陷等。因而,在保持其他因素相对不变的条件下,利用探测线圈测量涡流所引起的磁场变化,可推知试件中涡流的大小和相位变化,进而获得有关电导率、缺陷、材质状况和其他物理量(如形状、尺寸等)的变化或缺陷存在等信息。
涡流探伤通常能够在几秒钟内完成,这使得它易于整合到生产线中,并且,此过程不需要用到耦合剂,探伤之前也不需要对样品进行预清洗工作。此外,由于涡流还受电导率影响,这种技术还可以用来探伤合金材料之间的差异性等。
涡流探伤的应用范围
那么涡流探伤技术能够具体用来做什么呢?该技术能够在哪些方面帮助人们验证工业生产流程并降低不合格产品的生产概率呢?
下面列出了一些涡流探伤的主要应用范围:
1裂纹和缺陷探伤
涡流探伤技术非常适用于查找金属部件的表面裂缝和缺陷,探伤效率极高。在受到交变磁场诱导后,待探伤制品内将产生涡流流动,如果这些涡流被表面裂缝或者缺陷中断,涡流探头和仪器将会探测出涡流的变化并将该存有裂缝的制品标记为失效产品。
涡流探伤对于裂缝和缺陷来说,是一种非常干净、快速且探伤结果可重复的高效方法,而且很容易被整合到生产过程中,用于探伤一些利用肉眼难以察觉的缺陷。所用的探伤探针可以根据需求进行定制以有针对性的适应一些面积较小、难以触及的关键区域。此外,有了阵列探测器和材料处理系统的辅助还能够实现对一些大型或者复杂产品的表面区域进行探伤。
可以利用涡流探伤技术探伤缺陷的产品主要有:车轮轴承、滚子轴承、小齿轮、轴、传动齿轮、活塞、紧固件、管道系统以及钢轨等。
2热处理和材料结构验证
涡流探伤还能通过与已知结构的完好组件进行对比,进而验证待测试件是否具有完好的材料结构。
热处理过程中的变化以及所使用合金种类的不同都会导致材料结构的差异。这些差异会导致测试件表面硬度和硬化层深度的变化。涡流探伤技术能够通过材料电导率和磁导率的变化探伤出这些差异,因此,该技术有助于验证测试件的结构完整性和耐久性。
涡流探伤对于热处理和材料结构验证方面,属于一种快速、干净的探伤方法;对产品的探伤结果通常可以清晰的显示出“通过”或“不合格”。
可以利用涡流探伤技术进行热处理过程和材料结构验证的产品主要有:车轮轴承、滚子轴承、轴杆、小齿轮、球钉、金属粉末烧结产品、插销、紧固件、传动齿轮、传动系组件以及医疗器件等。
3螺纹、功能件和装配件验证
类似于上述结构测试,涡流探伤技术还能够用于验证螺纹的质量问题、组件的功能验证、或者验证某个装配件是否被正确地组装在一起。
对螺纹进行涡流探伤有助于识别出螺纹是否出现局部受损、尺寸是否过大或者过小、设计是否合理等信息。
可以利用涡流探伤进行功能验证的组件主要包括:门凹槽、齿条等。
装配件的验证测试主要包括:轴承座圈上球轴承的安装、轴承内的夹杂物、活塞环的取向以及阀门和管件的组装等。
涡流探伤的应用场合
在许多情况下,涡流探伤都能够取得很好的测试效果。
大批量测试:对于大批量生产测试,涡流探伤体系能够提供较高的投资回报率。
小批量测试:小批量测试方法比较适合于探伤具有较高经济价值的测试件或者其本身经济价值不高,但在某些情况下,质量的不合格会导致较大的经济损失的产品,例如,一个经热处理后的小型C型夹本身是一个成本低廉的产品,但是如果将其与汽车制动系统联用,那么由该产品不合格所引起的代价则会很高。
整合到生产线:对于在线涡流探伤而言,探伤速度和可重复性是两个非常关键的因素;当将该方法直接整合到生产线上,涡流探伤设备能够与可编程控制器共同协作快速找出不合格产品。
涡流探伤的操作
与其他探伤技术一样,如果不能正确的执行涡流探伤操作,那么得出的结果将会是不一致甚至是错误的。进行准确、可靠的测试要求涡流传感器(线圈/探针组装)与根据特定测试需求选取的低噪声涡流探伤设备相互匹配。此外,还需要一套良好的材料处理系统和一个具有基本的涡流探伤知识且接受过培训的专业操作人员。
操作具体包括哪些内容呢?
首先,你需要对可能会遇到的情况做好理解及准备工作。
对于材料结构或者热处理探伤试验,应当记录实际探伤环境,例如热量、风冷、感应加热线圈错位(由于线圈弯曲或者损坏等)等。了解测试组件表面、几何特性和取向是如何影响测试结果的;一般而言,粗糙、不平整的表面可能会引起额外的系统噪声,这就可能造成一些很小的缺陷难以被探伤出来。测试件的几何结构和取向等因素同样需要进行考虑。在测试过程中,应当确保涡流传感器(线圈/探针)相对于样品保持在同样的位置,如果间距或者位置不一致,测试结果也会不一致。
另外,需要一套可靠的材料处理系统。
再好的仪器和探伤探头也不能弥补工具不合适所带来的不足。定期的系统检查有助于确保测试组件和传感器保持在正确的位置上。如果测试是手动进行的,应该利用机械工具以减少不良的测试影响。
尽量采用稳定、低噪声的涡流探伤装置。
一般而言,设备噪声越低,所能探伤出的缺陷尺寸越小;材料间的差异也能更加清晰地凸显出来。系统稳定能够确保测量结果的一致性。
探伤操作人员一般要求具备基本的涡流探伤知识且接受过专业的岗前培训。
当测试条件发生改变或者出现一些突发故障时,这些训练有素的操作人员能够及时发现问题,并对其进行评估或者做出相应的调整,例如更换传感器等。在选择涡流探伤设备时,应尽量选择一款易于使用的设备;现在已有很多设备结合了现代触摸屏显示系统和直观的用户界面,这使得在员工流动率较高的今天,为新员工进行培训也变的更加容易。
值得一提的是,在选择购买一套涡流探伤系统之前,先对你经常要探伤的组件进行适当的测试和评估,一些涡流探伤系统供应商会提供免费的评估和测试报告来验证测试的可行性,因此在购买和安装前,先确定一个值得信赖的厂商并提前与他们进行互动和合作,以清楚了解该厂商生产的涡流探伤设备是否真的适合你今后的探伤工作。
涡流探伤技术主要是采用电磁场探伤金属制品表面和次表面上的缺陷。电磁感应科学是在19世纪中期发展而来,在19世纪后期,人们发现将线圈与具有不同电导率的金属接触时得到的实验数据会发生改变。在19世纪50年代到60年代,涡流技术逐渐发展成了一种广泛应用于核能和航空工业领域的新兴技术。
在涡流探伤技术中,将通电线圈放置在待探伤金属样品附近,金属样品内会感应出涡流。与不含缺陷的同种金属制品对比而言,制品中若存在缺陷或者结构发生改变都会导致涡流变化。因为涡流的分布和大小,除与线圈的形状和尺寸、电流的大小和频率等有关外,还取决于试件的电导率、磁导率、形状和尺寸、与线圈的距离以及表面有无裂纹缺陷等。因而,在保持其他因素相对不变的条件下,利用探测线圈测量涡流所引起的磁场变化,可推知试件中涡流的大小和相位变化,进而获得有关电导率、缺陷、材质状况和其他物理量(如形状、尺寸等)的变化或缺陷存在等信息。
涡流探伤通常能够在几秒钟内完成,这使得它易于整合到生产线中,并且,此过程不需要用到耦合剂,探伤之前也不需要对样品进行预清洗工作。此外,由于涡流还受电导率影响,这种技术还可以用来探伤合金材料之间的差异性等。
涡流探伤的应用范围
那么涡流探伤技术能够具体用来做什么呢?该技术能够在哪些方面帮助人们验证工业生产流程并降低不合格产品的生产概率呢?
下面列出了一些涡流探伤的主要应用范围:
1裂纹和缺陷探伤
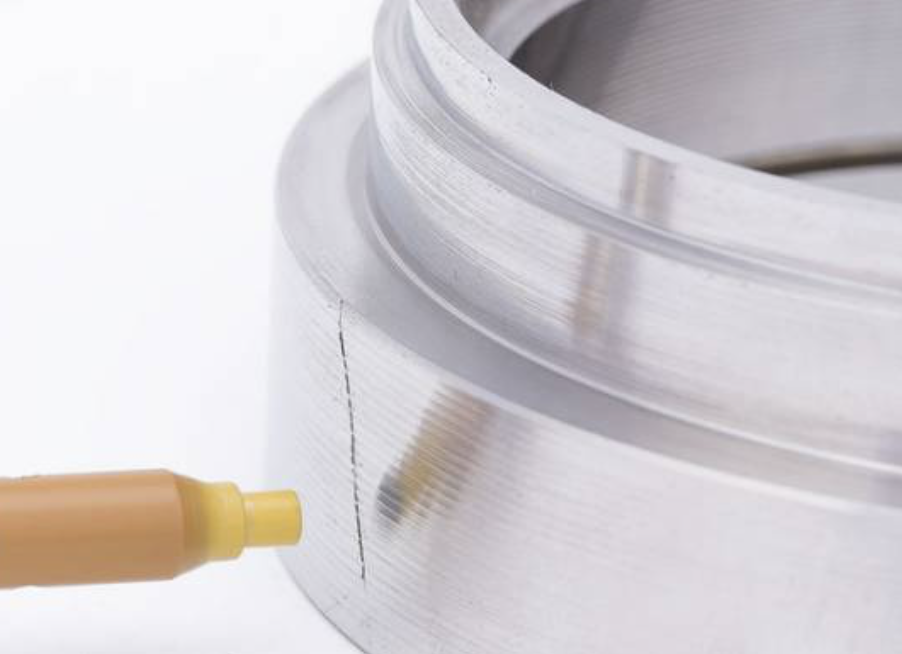
用于探伤裂缝的涡流探伤探针
涡流探伤技术非常适用于查找金属部件的表面裂缝和缺陷,探伤效率极高。在受到交变磁场诱导后,待探伤制品内将产生涡流流动,如果这些涡流被表面裂缝或者缺陷中断,涡流探头和仪器将会探测出涡流的变化并将该存有裂缝的制品标记为失效产品。
涡流探伤对于裂缝和缺陷来说,是一种非常干净、快速且探伤结果可重复的高效方法,而且很容易被整合到生产过程中,用于探伤一些利用肉眼难以察觉的缺陷。所用的探伤探针可以根据需求进行定制以有针对性的适应一些面积较小、难以触及的关键区域。此外,有了阵列探测器和材料处理系统的辅助还能够实现对一些大型或者复杂产品的表面区域进行探伤。
可以利用涡流探伤技术探伤缺陷的产品主要有:车轮轴承、滚子轴承、小齿轮、轴、传动齿轮、活塞、紧固件、管道系统以及钢轨等。
2热处理和材料结构验证
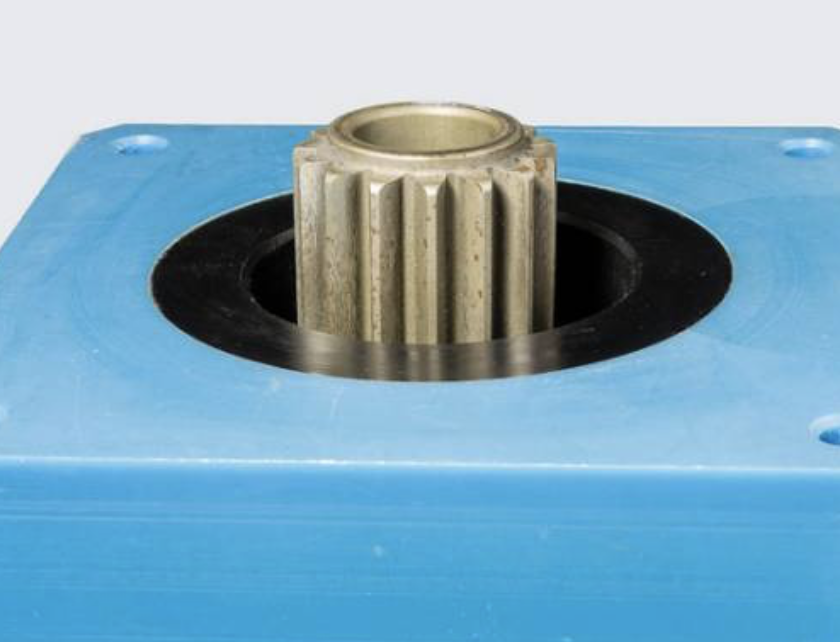
对热处理的齿轮进行涡流探伤
涡流探伤还能通过与已知结构的完好组件进行对比,进而验证待测试件是否具有完好的材料结构。
热处理过程中的变化以及所使用合金种类的不同都会导致材料结构的差异。这些差异会导致测试件表面硬度和硬化层深度的变化。涡流探伤技术能够通过材料电导率和磁导率的变化探伤出这些差异,因此,该技术有助于验证测试件的结构完整性和耐久性。
涡流探伤对于热处理和材料结构验证方面,属于一种快速、干净的探伤方法;对产品的探伤结果通常可以清晰的显示出“通过”或“不合格”。
可以利用涡流探伤技术进行热处理过程和材料结构验证的产品主要有:车轮轴承、滚子轴承、轴杆、小齿轮、球钉、金属粉末烧结产品、插销、紧固件、传动齿轮、传动系组件以及医疗器件等。
3螺纹、功能件和装配件验证
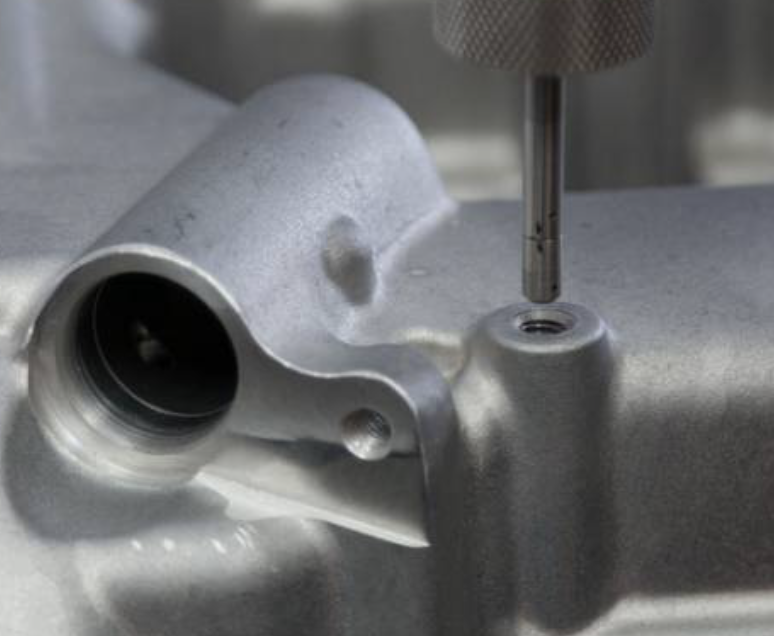
对螺纹进行涡流探伤
类似于上述结构测试,涡流探伤技术还能够用于验证螺纹的质量问题、组件的功能验证、或者验证某个装配件是否被正确地组装在一起。
对螺纹进行涡流探伤有助于识别出螺纹是否出现局部受损、尺寸是否过大或者过小、设计是否合理等信息。
可以利用涡流探伤进行功能验证的组件主要包括:门凹槽、齿条等。
装配件的验证测试主要包括:轴承座圈上球轴承的安装、轴承内的夹杂物、活塞环的取向以及阀门和管件的组装等。
涡流探伤的应用场合
在许多情况下,涡流探伤都能够取得很好的测试效果。
大批量测试:对于大批量生产测试,涡流探伤体系能够提供较高的投资回报率。
小批量测试:小批量测试方法比较适合于探伤具有较高经济价值的测试件或者其本身经济价值不高,但在某些情况下,质量的不合格会导致较大的经济损失的产品,例如,一个经热处理后的小型C型夹本身是一个成本低廉的产品,但是如果将其与汽车制动系统联用,那么由该产品不合格所引起的代价则会很高。
整合到生产线:对于在线涡流探伤而言,探伤速度和可重复性是两个非常关键的因素;当将该方法直接整合到生产线上,涡流探伤设备能够与可编程控制器共同协作快速找出不合格产品。
涡流探伤的操作
与其他探伤技术一样,如果不能正确的执行涡流探伤操作,那么得出的结果将会是不一致甚至是错误的。进行准确、可靠的测试要求涡流传感器(线圈/探针组装)与根据特定测试需求选取的低噪声涡流探伤设备相互匹配。此外,还需要一套良好的材料处理系统和一个具有基本的涡流探伤知识且接受过培训的专业操作人员。
操作具体包括哪些内容呢?
首先,你需要对可能会遇到的情况做好理解及准备工作。
对于材料结构或者热处理探伤试验,应当记录实际探伤环境,例如热量、风冷、感应加热线圈错位(由于线圈弯曲或者损坏等)等。了解测试组件表面、几何特性和取向是如何影响测试结果的;一般而言,粗糙、不平整的表面可能会引起额外的系统噪声,这就可能造成一些很小的缺陷难以被探伤出来。测试件的几何结构和取向等因素同样需要进行考虑。在测试过程中,应当确保涡流传感器(线圈/探针)相对于样品保持在同样的位置,如果间距或者位置不一致,测试结果也会不一致。
另外,需要一套可靠的材料处理系统。
再好的仪器和探伤探头也不能弥补工具不合适所带来的不足。定期的系统检查有助于确保测试组件和传感器保持在正确的位置上。如果测试是手动进行的,应该利用机械工具以减少不良的测试影响。
尽量采用稳定、低噪声的涡流探伤装置。
一般而言,设备噪声越低,所能探伤出的缺陷尺寸越小;材料间的差异也能更加清晰地凸显出来。系统稳定能够确保测量结果的一致性。
探伤操作人员一般要求具备基本的涡流探伤知识且接受过专业的岗前培训。
当测试条件发生改变或者出现一些突发故障时,这些训练有素的操作人员能够及时发现问题,并对其进行评估或者做出相应的调整,例如更换传感器等。在选择涡流探伤设备时,应尽量选择一款易于使用的设备;现在已有很多设备结合了现代触摸屏显示系统和直观的用户界面,这使得在员工流动率较高的今天,为新员工进行培训也变的更加容易。
值得一提的是,在选择购买一套涡流探伤系统之前,先对你经常要探伤的组件进行适当的测试和评估,一些涡流探伤系统供应商会提供免费的评估和测试报告来验证测试的可行性,因此在购买和安装前,先确定一个值得信赖的厂商并提前与他们进行互动和合作,以清楚了解该厂商生产的涡流探伤设备是否真的适合你今后的探伤工作。